I’ve posted two custom parts for the MPCNC: a wire harness and a customizable end-stop holder.
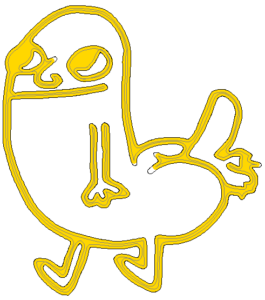
I tried a test run of the Optimal Fabrication Test Model (it’s dickbutt…we talked about this).
Results were…mixed. It started out strong by making key outline portions, so I left the room. I came back when I heard the spindle inexplicably struggling from downstairs. I come back to find the spindle has sunk all the way into the foam, and the nut that mounts the endmill to the tool has itself ground a sizable trench through the foam. Bits of foam are everywhere.
It turns out two separate failures happened. First, the Z coupler came loose…that’s my fault, as the plans called for nylon locknuts, but I couldn’t find any locally, so I used plain hex nuts, so the screws tightening it vibrated loose. Locknuts: ordered.
Second, there was a flaky connection on the X-axis, which is why it’s a vertical trench instead of a vaguely dickbutt-shaped trench. Apparently the wire I used doesn’t like to crimp well in Dupont connectors, so I crunched them all harder and added a bit of solder to be sure.
I 3D printed a pen holder to attach to the tool, so I can do ink-based tests while I work out the kinks. I did a dickbutt print on the same crappy foam, offsetting it a bit upward. The result is surprisingly good, given that the foam is nowhere near level, and I used the same program that assumes a 1/8″ endmill. Look at the solid ink on those eyes…nice!